¿Es posible un cambio de matriz en menos de 10 minutos? La técnica Single Minute Exchange of Die permite ahorrar tiempo en los set-up mediante el trabajo con lotes más pequeños. ¿Quiere saber qué es SMED?
El SMED es una técnica, como decimos, que trata de optimizar las operaciones en los set-up. Se pretende simplificar los procesos y, sobre todo, convertir el mayor número de tareas en “externas”.
Es decir, que estas actividades puedan realizarse sin interrumpir la producción que se lleva a cabo en cada momento. De esta forma, se pueden conseguir grandes beneficios que le contamos más adelante.
Siga leyendo este post sobre qué es SMED para profundizar en esta parte de la logística. Y si su interés profesional está enfocado en esta área, le animamos a que se informe sobre nuestra Maestría en Logística, Compras y Transporte para profesionalizarse en este ámbito.
SMED en siete etapas
Single Minute Exchange of Die se presenta como una técnica o herramienta para la mejora continua. Las empresas que no se detienen y cuentan con ambiciones de crecimiento deben tomar en cuenta esta forma de actuar en los entornos productivos con maquinaria.
Implementando esta metodología el doctor Shigeo Shingo pretendía reducir los tiempos de preparación a menos de 10 minutos. Aunque puede que esto no siempre sea posible en todos los procesos, la idea de minimizar el tiempo es lo relevante de esta técnica.
A continuación vamos a detallar los siete pasos que debe seguir una compañía para poner en marcha esta técnica y conseguir ahorrar tiempo.
Etapa 1: preparación previa
Esta etapa puede subdividirse en dos fases: investigación y creación de un equipo. La primera, se basa en conocer el producto, las operaciones, la maquinaria, el layout de la fábrica, el modo de trabajo,…
Es decir, es una fase de conocer profundamente cómo funciona el proceso en términos materiales y, por supuesto, teniendo en cuenta los tiempos de preparación. Para ello, no se olvide de revisar sus datos históricos y realizar una observación en directo.
La segunda fase de esta primera etapa es construir un equipo. Este debe contar con conocimientos especializados sobre Lean Manufacturing y, más concretamente, sobre los fundamentos de esta metodología. El grupo deberá incluir profesionales con capacidades para realizar modificaciones técnicas y organizativas.
Además, para iniciar la implementación de esta técnica hay que supervisar que tengamos los medios necesarios. Por ejemplo, planos de distribución de la planta, papel y lápiz para realizar anotaciones, videocámaras para grabar los procesos, una sala de reuniones.
Etapa 2: análisis de la actividad
Es el momento de realizar grabaciones de cada una de las actividades que forman parte de un proceso de cambio de referencia. Igualmente, cada persona implicada debe ser filmada.
El vídeo se debe extender desde que se fabrica la última pieza de referencia saliente y finalizará cuando se inicie la fabricación de la pieza de referencia entrante. No obstante, si no extraemos una pieza OK, el proceso continúa en modo preparación.
Cuando ya tenemos todas las grabaciones listas, el equipo debe retirarse a la sala de reuniones para visualizar y realizar un análisis sobre lo observado.
Etapa 3: diferenciar y separar interno de externo
La clave del éxito de esta técnica es la separación de las tareas internas y externas para conseguir el ahorro de tiempo. Para ello, todos los implicados en los procesos deben identificarlas en ambas categorías:
- Internas: se trata de tareas que se llevan a cabo con el equipo completamente detenido o con una velocidad menor a la habitual. Estas están asociadas al set-up.
- Externas: igualmente, están asociadas al set-up pero se realizan con el equipo a una velocidad normal.
Por otra parte, en esta fase podemos aprovechar para descubrir cuáles son las tareas innecesarias. Es decir, que no tienen que ver con el proceso de set-up y pueden ser eliminadas.
Etapa 4: organización de las actividades externas
En este momento se lleva a cabo la planificación de las actividades externas con el fin de que estén listas en el momento de cambio de referencia. Podemos realizar una lista con las consideraciones más importantes:
- Preparaciones previas.
- Herramientas y piezas necesarias para el cambio.
- Colocación de herramientas.
- Supervisión de las piezas y herramientas.
- Modo de transporte de las piezas.
Estas son solo algunas de las cuestiones que puede incluir en su check-list en la cuarta etapa.
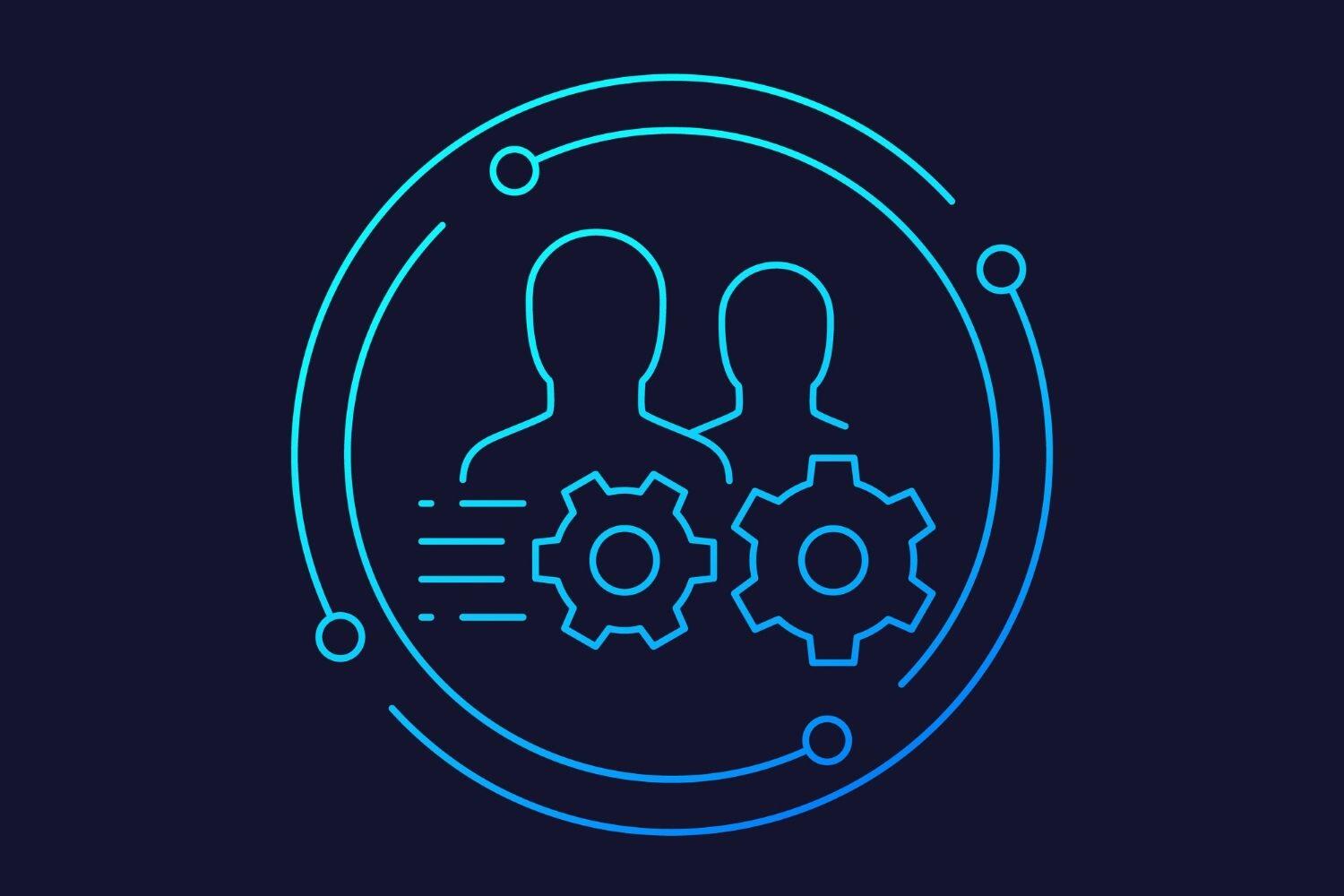
Etapa 5: transformar las tareas internas en externas
Como hemos mencionado, el objetivo es conseguir las máximas tareas externas. Ya que estas permiten mantener el movimiento mientras se realiza el cambio. Para ello, hay que definir un plan de acción para realizar esta conversión.
Por lo tanto, deberá indicarse la acción, la persona que la realiza y cuándo debe acabar dicha tarea.
Etapa 6: reducción de tiempos en las tareas internas
Dado que se trata de las actividades donde debemos parar el movimiento, el objetivo es reducirlas al máximo. Hay que pensar cómo mejorar, elaborar un plan de acción y, después, implementarlas. Igual que en la etapa anterior, hay que definir qué hacer, quién lo hace y en qué
Etapa 7: seguimiento del proceso SMED
Una vez que hemos terminado la implementación, es fundamentar realizar un seguimiento posteriormente. Pudiendo comprobar así que todo está funcionando correctamente y no hay desviaciones. En el caso de haberlas, podrán tomarse acciones de corrección. Habitualmente hay dos formas:
- Registrar incidencias semanalmente.
- Registrar los tiempos de cambio semanalmente y realizar gráficos que muestren las deviaciones.
Beneficios de la técnica SMED
El objetivo de esta técnica es reducir los tiempos, por lo tanto, a la misma vez es su ventaja más significativa. Pero esto supone un ahorro de costos del set-up así como aumentar la flexibilidad.
Permite modificar el tamaño de los lotes para trabajar con unos más pequeños. Igualmente con los inventarios, reduciendo el stock y pudiendo liberar parte del capital inmovilizado.